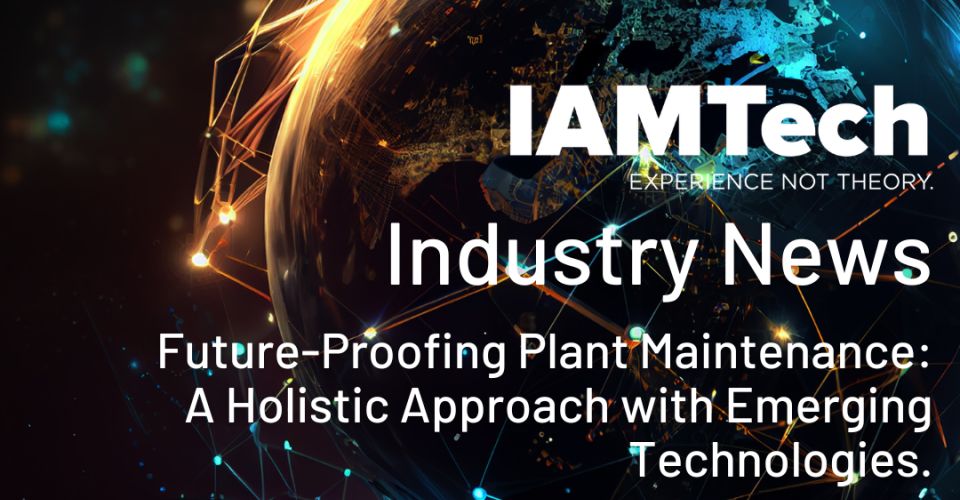
“You need to act now to understand where you are and where you can travel to. It’s a holistic approach and understanding energy efficiency is a key starting point of getting on the road that’s going to take you in the right direction.” - Ian Lucas, 2M Group of Companies (NEPIC Asset Management Conference Panel Discussion).
The IAMTech team recently participated in the NEPIC Asset Management Conference held at Hardwick Hall in Teesside.
Teesside, known for its industrial heritage dating back to the prosperous ICI era of the 1990s, now faces the challenge of aging assets and escalating maintenance expenses in the 2020s.
Speakers at the event highlighted the pressing need for a comprehensive approach to plant maintenance, signalling a departure from traditional reactive methods. Instead, there is a growing emphasis on proactive measures to achieve operational excellence, necessitating a paradigm shift in maintenance strategies.
Today's landscape demands a holistic approach that not only predicts and prevents failures but also prioritises safety, environmental sustainability, and efficiency. At the core of this approach lie innovative technologies poised to revolutionise maintenance practices. This article explores these strategies, highlighting the seamless fusion of established best practices with cutting-edge solutions to safeguard the future of plant maintenance.
The Evolution of Maintenance Strategies
The evolution from reactive to proactive maintenance underscores the industry's recognition of the inefficiencies inherent in waiting for equipment to fail. The holistic approach builds on this foundation, integrating:
- Preventive Maintenance: Regular, scheduled maintenance tasks designed to prevent equipment failure before it occurs. This strategy relies on historical data and manufacturer recommendations to plan interventions, thus reducing unplanned downtime and extending equipment lifespan.
- Predictive Maintenance: Leveraging advanced analytics, IoT sensors, and real-time data monitoring to predict equipment failures before they happen. This approach optimises maintenance schedules based on actual equipment condition rather than predefined schedules, further reducing downtime and maintenance costs.
- Condition-Based Maintenance: Like predictive maintenance, this strategy involves monitoring the operational condition of equipment during its normal operation. By continuously analysing data from sensors, maintenance can be performed when certain indicators show signs of decreasing performance or an impending failure.
- Reliability-Centred Maintenance (RCM): This strategy focuses on maintaining the inherent reliability of equipment, identifying the functions and elements critical to plant operation. RCM involves a detailed analysis to determine the most effective maintenance strategies to ensure equipment reliability and safety.
Best Practices in Maintenance
Adopting a holistic approach requires not just the right strategies but also adherence to best practices that ensure these strategies are effectively implemented:
- Comprehensive Training: Ensuring that maintenance and operational staff are fully trained in the latest practices and technologies. This includes understanding not just the functionalities of software tools, but also how their application can enable as the principles of predictive and reliability-centred maintenance.
- Data-Driven Decision Making: Utilising data analytics to inform maintenance decisions. This involves collecting and analysing data from various sources, including equipment sensors, maintenance logs, and software systems, to identify patterns, predict equipment failures, and optimise maintenance schedules.
- Integrated Safety Measures: Incorporating safety into every aspect of the maintenance process, from planning and execution to review and improvement. Emerging software systems over the last decade, including IAMTech's Permit To Work software IAMPermit, can be a part of the jigsaw to enable this , ensuring that every maintenance task is carried out with the highest safety standards in mind.
- Sustainability Considerations: Aligning maintenance strategies with environmental and sustainability goals. This includes minimising waste, optimising energy use, and choosing environmentally friendly materials and methods whenever possible.
Integrating Emerging Technologies for Optimal Maintenance
The integration of IoT, AI, and ML software can create a powerful ecosystem for predictive and condition-based maintenance minimising unexpected failures and extending the lifespan of equipment.
IAMTech's iPlanMAINTAIN & iPlanSTO software systems, help to streamline the management of complex maintenance projects, such as shutdowns, turnarounds, and outages, ensuring they are completed on time and within budget, minimising downtime, and maximising plant productivity.
Real-time monitoring and data analysis offer unprecedented insights into equipment health, allowing for timely interventions that prevent failures and optimise maintenance schedules. Technological enhances a holistic maintenance strategy, ensuring that plants operate safely, efficiently, and sustainably.
Understanding Energy Efficiency in Asset Management Strategy
Energy efficiency is not merely a desirable attribute but a crucial component of an effective asset management strategy. Recognising the significant impact of energy consumption on operational costs and environmental sustainability, plants are increasingly prioritising energy efficiency in their maintenance practices.
By optimising energy usage through proactive maintenance measures, such as equipment upgrades, process optimisation, and predictive maintenance, plants can reduce energy waste, lower operating costs, and minimise their carbon footprint. Moreover, integrating energy efficiency considerations into asset management strategies enhances overall operational resilience by mitigating risks associated with volatile energy prices and regulatory changes. As the importance of sustainability and cost-efficiency continues to grow, a comprehensive understanding of energy efficiency is indispensable for maximising the longevity and performance of industrial assets.
Navigating Challenges
Adopting these advanced technologies and strategies comes with its set of challenges, including the upfront costs, the need for cultural change towards digital adoption, and ensuring data security. Overcoming these challenges requires a strategic approach, emphasising the long-term ROI of reduced downtime and maintenance costs, fostering a culture of continuous learning and improvement, and implementing robust cybersecurity measures to protect sensitive data.
The Future of Plant Maintenance
As we look towards the future, the integration of holistic maintenance practices with advanced technologies like IAMTech's industrial software solutions is set to become the standard.
This approach not only ensures operational excellence but also aligns with broader goals of safety, sustainability, efficiency, and resilience. By embracing these strategies and best practices early, plants and facilities can ensure they are not just keeping pace with the growing demands of today but are also future proofing their operations for the challenges of tomorrow.
As the industry continues to evolve, the commitment to ongoing improvement and adaptation will be key. The holistic approach to maintenance, empowered by technological advancements, will not only safeguard the operational integrity of plants but will also contribute to a more sustainable and productive industrial landscape. In this new era of maintenance, the goal is clear: to achieve a seamless blend of human expertise and technological innovation, driving towards a future where every plant operates at its peak potential.