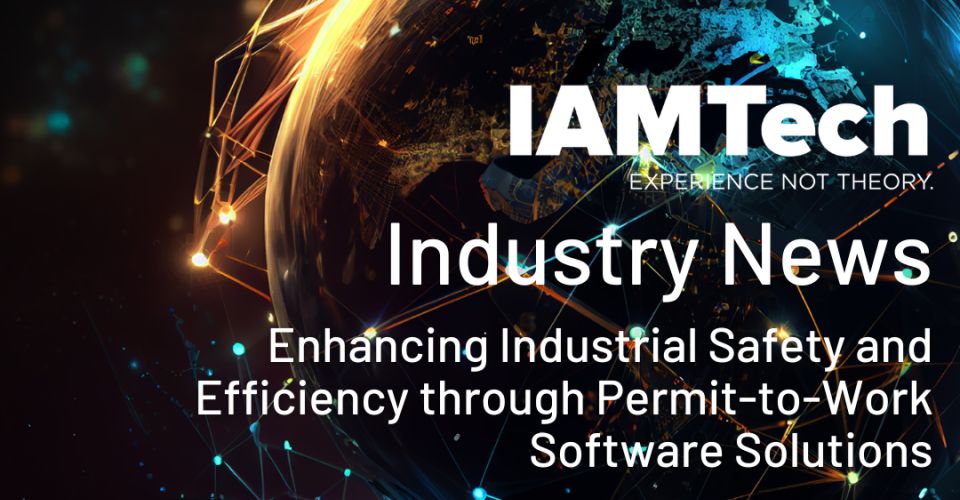
The concept of work control permits emerged in the early 20th century, pioneered by the US Navy to enhance safety protocols during ship repairs. Recognising that tasks like hot work and welding posed substantial risks, the Navy established a permit system that specified required tasks, identified potential hazards, and detailed essential safety measures. Over time, industries with high-risk environments—such as chemical processing and nuclear facilities—adopted similar permit-to-work (PTW) systems to manage hazardous tasks effectively.
Since then, PTW systems have been integral to risk management in high-risk industries. However, most industries, including oil and gas, petrochemicals, and manufacturing, still rely on the original paper-based format introduced over a century ago. While traditional paper-based PTW systems have proven effective and widely understood, they also present significant challenges, including workflow inefficiencies, tracking difficulties, and risks of document loss. Such issues have directly impacted organisational safety standards and worker protection.
In fact, traditional PTW systems have been implicated in more than 20% of maintenance-related incidents across several sectors, highlighting the need for a new approach to permit management to ensure safer and more efficient operations.
Following a prolonged period of limited advancement, the PTW system has recently seen rapid development, largely due to breakthroughs in digital technology. The first electronic PTW systems were introduced in the early 1990s in the UK petrochemical sector, as industry leaders recognised the limitations of paper-based systems in managing complex safety protocols. Digital PTW systems were initially adopted by major oil operators in the North Sea and then spread to the Middle East, where high-stakes operational environments demanded rigorous safety and coordination standards. Supported by industry collaboration and significant investment from major organisations, electronic PTW (ePTW) systems have now evolved to effectively replace and improve upon traditional paper-based methods.
Today’s ePTW solutions offer seamless integration with existing industrial processes, significantly improving safety compliance and enhancing overall operational efficiency.
This article delves into the specific benefits, challenges, and real-world applications of PTW software within industrial settings, featuring case studies from oil refineries and petrochemical industries. It’s essential reading for businesses still navigating the transition from paper-based systems.
Structure and Function of Permit-to-Work Software Systems
Real-world studies reveal that issues such as inconsistent application of procedures and human error often lead to safety risks. The catastrophic event that occurred on the Piper Alpha offshore oil and gas platform and killed 167 workers was attributed mainly to human error including deficiencies in the permit-to-work (PTW) system (ScienceDirect.com):
- PTW software systematically reduces these risks by embedding safety protocols and regulatory requirements into each digital permit, thereby ensuring uniform application and improving compliance. A permit-to-work system provides a structured approach to hazardous work by outlining tasks, assessing risks, and specifying safety controls to mitigate risks.
- The transition to software-based PTW is particularly significant in industries where overlapping tasks and complex hazardous activities are frequent, allowing digital systems to monitor, communicate, and streamline these operations effectively IChemE Symposium Series 139 (1995).
Benefits of Digital Permit-to-Work Systems
The benefits of PTW software are far-reaching, offering advancements in safety, compliance, monitoring, and workflow management:
- Improved Safety and Regulatory Compliance: PTW software integrates safety checks, ensures compliance with regulatory standards, and reduces risks through real-time, role-based authorization. A case study in an Iranian oil refinery demonstrated that digital PTW systems decreased the frequency of maintenance-related accidents by ensuring that permits addressed detailed risk assessments and comprehensive safety protocols for each task. This improvement in safety compliance was especially beneficial in environments where multiple safety layers were required to protect both personnel and operational equipment (Mousavi, S.M et al).
- Enhanced Real-Time Monitoring and Remote Access: Unlike paper-based systems, PTW software enables instant access to all permits, providing managers with remote monitoring capabilities across multiple locations. This feature is essential for large industrial plants with geographically dispersed operational areas. In a study of Kuwaiti oil fields, the e-PTW system provided operators with a digital dashboard, allowing real-time monitoring of all active permits, simplifying compliance checks, and reducing delays in permit issuance and approval processes IJISET_V2_I4_77.pdf.
- Improved Workflow Coordination and Communication: Permits are an effective means of communication among site managers, plant supervisors, and operators, and the individuals who undertake the work. Paper-based systems lack the safety nets that technology provides, for instance, a breakdown in the PTW system at shift change over and in the safety procedures was one of the major factors that resulted in the Piper Alpha disaster. PTW software promotes transparency and streamlines communications among operational teams, supervisors, and safety officers. A study conducted by the Health and Safety Laboratory (HSE) on smaller chemical plants in the UK demonstrated that digital systems reduced procedural delays by automating alerts for permit approval and expediting handovers during shift changes. This real-time coordination was vital for synchronizing tasks, especially in environments with complex simultaneous operations IChemE Symposium Series 139 (1995).
- Data Traceability and Auditability: Digital PTW systems offer complete traceability of the permit lifecycle, facilitating internal audits and post-incident investigations. For example, a review of PTW systems in Indonesian geothermal power plants showed that digital permit data helped pinpoint procedural deficiencies and identify points of human error in incident cases. The system’s audit trail was crucial for safety reviews, demonstrating the significant role of PTW software in post-incident evaluations and continual safety improvement (Sudarmo, Y.R et al).
Industry-Specific Applications and Case Studies
- Oil and Gas Sector: Oil and gas companies were among the earliest adopters of PTW software, using it to manage extensive maintenance and operational tasks across remote sites. In Kuwait, the shift to an electronic PTW system resulted in a more than 20% reduction in permit processing time, significantly enhancing safety compliance and reducing risks associated with confined space entries and hot work activities. This shift enabled operators to pre-emptively address risks through enhanced hazard identification and procedural checks embedded within the software IJISET_V2_I4_77.pdf.
- Chemical Manufacturing: In chemical plants, where high levels of hazardous materials necessitate strict control measures, PTW software helps reduce incidents by ensuring consistent hazard identification and risk management. The Health and Safety Executive (HSE) in the UK identified that, in smaller chemical plants, inadequate permit systems contributed to maintenance incidents. A survey revealed that nearly 30% of permits lacked detailed hazard identification, underscoring the need for digital solutions that enforce structured, uniform protocols across all tasks and reduce reliance on individual decision-making IChemE Symposium Series 139 (1995).
- Petrochemical Industry: A case study from Iran’s petrochemical sector highlighted the role of PTW software in mitigating maintenance-related hazards in refineries. The study noted that the implementation of PTW software improved task-specific hazard identification, risk assessment, and documentation, addressing over 60% of previously identified safety deficiencies. The digital system’s real-time monitoring capabilities facilitated risk control during critical maintenance, reducing risks associated with potential leaks, fires, and other operational hazards (Mousavi, S.M et al).