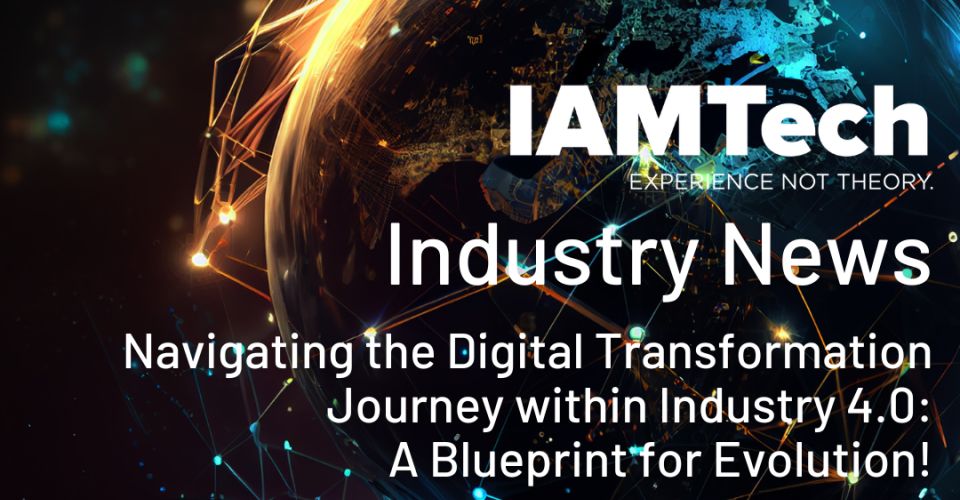
The fourth industrial revolution is upon us, and it’s marked by a broad range of technologies blurring the lines between the physical (equipment & personnel) & digital spheres.
In the rapidly evolving landscape of Industry 4.0, the transition towards digitalisation is not just a trend but a strategic necessity for organisations in the production and manufacturing sectors.
Whilst the need for digital transformation in plant processes is becoming increasingly paramount, the landscape of digital transformation is vast, with a plethora of technologies promising to revolutionise how we conceive, manage, and execute operations.
From IoT devices collecting real-time data at unprecedented scales to AI-driven analytics predicting maintenance needs before they become critical, the options are as promising as they are overwhelming.
This abundance of technological solutions, while empowering, poses a significant challenge for industry leaders: knowing not only where to start but how to start and with which technologies to begin their digital transformation journey.
This article aims to provide a blueprint for organisations about to take their first steps into digital transformation, we hope you find it useful.
The Imperative for Digital Transformation
Let's start with the ‘why?’, the reasons behind the need for digital transformation. Many organisations hesitate to embark on the journey of digitalisation, clinging to the adage, "if it isn’t broke, don't fix it." This mindset prevails especially in sectors where traditional operations have yielded profitability for years.
However, it's essential to recognise the multitude of benefits digitalisation brings, not just to the industry at large but specifically to your organisation. The past success of non-digital operations doesn't negate the potential for significant enhancement through digital transformation. This shift represents a fundamental change in how an organisation delivers value to its customers, offering a pathway to not only optimise operations but also to fundamentally redefine them.
For industries focused on production and manufacturing, adopting digital technologies is key to boosting operational efficiency, enhancing safety, and mitigating environmental impacts.
The push towards digitalisation is propelled by several critical factors, including fluctuating market conditions, escalating regulatory demands, and the paramount importance of operational resilience.
Be warned, organisations that lag behind in their adoption of digital advancements risk being outperformed by early adopters in the foreseeable future!
Where to Start: Assessing Your Digital Maturity
The starting point for any digital transformation journey involves a comprehensive assessment of the organisation's current digital maturity. This assessment helps identify process inefficiencies, data silos, and areas where digital technologies can drive significant improvements.
For industries dealing with complex assets and operations, such as oil and gas or power generation, this step is crucial in prioritising initiatives that offer the highest return on investment.
In short, what are your biggest pain points and where are you losing the most money?
How to Start: Building a Strategic Roadmap
Developing a strategic roadmap for digital transformation requires a clear vision of the desired future state and a detailed plan for achieving it. This involves setting measurable goals, identifying key digital initiatives, and aligning them with the overall business strategy.
It's essential to involve stakeholders from across the organisation in this process to ensure buy-in and facilitate a smoother implementation. A practical approach is to begin on a smaller scale by developing a business case for deploying a specific technology designed to address one of the major challenges identified earlier.
Remember, digitalisation should be approached incrementally. Attempting too much too quickly can lead to confusion, inefficiency, unnecessary expenses, and possibly complete failure of the innovation!
What to Start With: Selecting the Right Technologies
Choosing the right technologies is critical to the success of digital transformation efforts. In the context of Industry 4.0, this often involves the adoption of ERP’s (Enterprise Resource Planning), IoT (Internet of Things) devices, AI (Artificial Intelligence) and machine learning algorithms, digital twins, and blockchain technology.
IAMPermit, a digital work permit system, provides organisations who are still using a carbon paper-based permit system with good place to start on their digitalisation journey. IAMPermit allows you to administer permits in real-time reducing lengthy delays and keeps detailed records of permits issued, vital for auditing and compliance. It is also packed with features such as anti-clash detection and is even linked to google maps showing you the location of each permit on site on any given day.
These solutions exemplify how targeted digital tools can address specific challenges within production and manufacturing industries, serving as catalysts for broader digital transformation initiatives such as iPlanSTO and iPlanMaintain. iPlanMaintain offers a digital framework for scheduling routine maintenance, whilst iPlanSTO, is a comprehensive shutdown, turnaround, and outage project management tool, enabling organisations to plan, manage, and execute complex projects with greater efficiency and visibility.
These more comprehensive industrial software systems enable organisations to plan, manage, and execute complex projects with greater efficiency and visibility.
Incorporating these technologies into existing workflows may seem overwhelming, but a thorough approach to research and evaluation is key.
Leading technology providers understand that this is a gradual process and typically do not expect immediate commitments. It's advisable to arrange for a live demonstration of the products and to include critical team members in the evaluation process.
Key Stakeholders, Maintenance Managers, and Procurement personnel, among others, will offer diverse insights on the products, which are crucial for making an informed decision.
Protect yourself: Cybersecurity.
The imperative for robust cybersecurity measures in industry cannot be overstated. As organisations increasingly integrate digital technologies into their operational fabric, they also open new vectors for cyber threats.
These advancements, while driving efficiency and innovation, can potentially expose critical infrastructure, sensitive data, and proprietary processes to cyber-attacks. The repercussions of such breaches are not only financial but can also include operational downtime, loss of customer trust, and damage to brand reputation.
Therefore, implementing stringent cybersecurity protocols is essential to safeguard the digital and physical assets of industries!
Overcoming Challenges: A Continuous Journey
The path to digital transformation is fraught with challenges, including cultural resistance, data privacy concerns, and the need for upskilling employees.
Overcoming these obstacles requires a concerted effort, continuous learning, and adaptability. It's also essential to measure progress and iterate on strategies as needed to ensure they remain aligned with changing industry dynamics and technological advancements.
Conclusion
Digital transformation in the oil, gas, chemical, mining and power industry’s is not a destination but a continuous journey of improvement, innovation, and adaptation. By understanding where to start, how to proceed, and which tools to leverage, organisations can navigate this journey more effectively.
Software solutions such as iPlanMaintain, iPlanSTO and IAMPermit not only facilitate specific aspects of this transformation but also exemplify the potential of digital technologies to revolutionise industry practices.
As we move forward into Industry 4.0, embracing digitalisation will be pivotal in ensuring sustainability, efficiency, and competitiveness. Start early and start small!