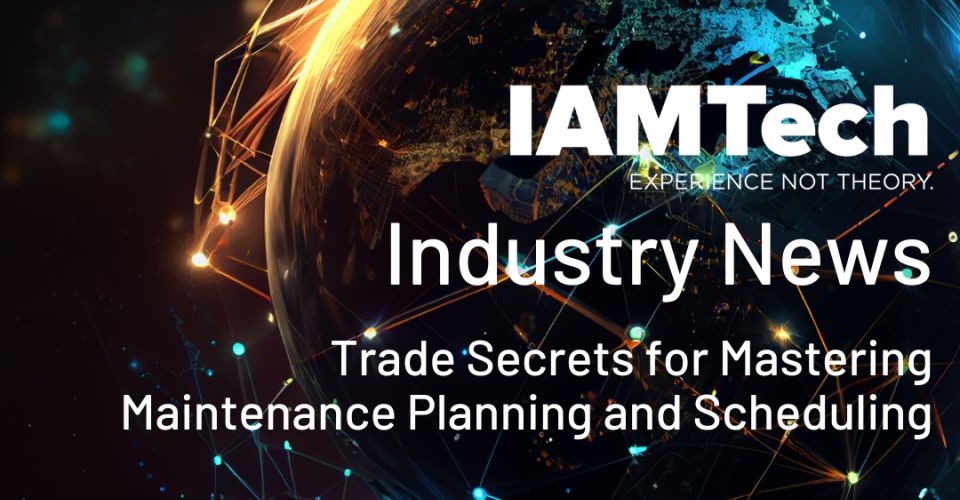
When considering your maintenance operations, effective planning and scheduling are essential for enhancing efficiency and profitability while maintaining the highest possible HSE standards.
Despite the apparent simplicity of the underlying concepts such as, acknowledging human imperfection, ensuring workers have enough tasks, and recognising that not all new reactive work requires immediate action - many organisations struggle with implementation.
In organisations that take a reactive approach to maintenance, planning and scheduling can often be viewed as more of a hindrance than a help. This approach overwhelms maintenance teams with reactive tasks resulting in their approach to planning being considered an unnecessary as a burden that wastes labour resources.
However, in teams that adopt a proactive approach to maintenance, proper planning and scheduling can transform these frustrations into opportunities for improvement.
Planning for Success
One major challenge in maintenance operations is planning individual work orders. Historically, maintenance workers relied on their skills, experience and knowledge to solve problems independently, so the sudden shift to relying on planners can be met with resistance.
To combat opposition, management often promises perfect plans that eliminate the need for searching for parts; this can, however, result in unrealistic expectations. Resulting from this misconception, when issues do arise, maintenance workers tend to blame planners and demand immediate assistance.
Instead, acknowledging that no one is perfect, including job plans, is crucial for effective planning. This approach, theorised by Dr. Edwards Deming, an American management consultant, suggests that by recognising and addressing imperfections organisations allow for continuous improvement. Steven Bartlett also discusses this concept in his new book The Diary of a CEO (2023); wherein the 1950s, American companies largely ignored Deming's advice, while Japanese companies like Toyota embraced it. As a result, Japanese car manufacturers surpassed their American counterparts achieving global success through continuous feedback and improvement.
To address the frustrations of planning and to allow for imperfections, it’s first beneficial to redefine the role of planners within your organisation. Instead of aiming for perfect plans, planners should instead act as "Maintenance Historians". In this way planners become instrumental in providing head starts by clarifying operator requests and saving this information for future reference. This approach works especially well when maintenance workers provide regular feedback. By organising an organisations’ “Information Archive” planners benefit all maintenance workers additionally improving and developing the planning process over time.
A Schedule as a Goal not a To-do List
Scheduling is another area of plant maintenance where common-sense principles can make a significant difference.
Initial efforts to create detailed daily schedules can often prove impractical due to the dynamic nature of maintenance work. In addition, scheduling work can often feel like a constant pull between schedule compliance and productivity. Do you underload the schedule to come in under target or overload them to stretch for maximum productivity from the teams? How much work is the right amount?
The trick is to change your perception of ‘The Schedule’.
Rather than seeing the purpose of a schedule as simply a task to complete throughout the week, view the schedule as a goal. Instead of a ‘to do list’ the schedules’ true purpose becomes maximising the productivity of your maintenance teams.
So, with this in mind, how much work is the right amount? Well, ‘aim for the stars, land on the moon’. Giving your maintenance team a fully loaded schedule might not help you to hit your schedule compliance targets, but you will soon see a difference in your backlog.
This approach is based on the simple principle, often termed Parkinsons Law, i.e. ‘Work expands to fill the time allotted for its completion’. Providing maintenance crews with a full week's worth of work has been shown to significantly boost productivity and address backlogs effectively. By ensuring crews have a full workload, productivity increases, and the backlog is reduced, even with modest schedule compliance.
How does this work with Reactive Work
Reactive work, which often bypasses planning to avoid delays, poses further challenges. Recognising that not all reactive work needs to start immediately allows for better planning and scheduling of these tasks. Reactive maintenance tasks that are perhaps postponed by a day, two days etc can be planned and scheduled. By creating quick job plans for non-emergency tasks and incorporating feedback, planners can streamline processes and improve overall efficiency. Additionally, planners can catalogue and organise these maintenance tasks for future reference by maintenance teams.
Conclusion
Although planning and scheduling in maintenance operations can be challenging overcoming difficulties regularly hinge on simple common-sense principles. Acknowledge human imperfection, redefine planners as historians, ensure workers have enough tasks, and plan reactive work without delaying immediate tasks. By applying these principles, plants can achieve significant productivity gains and enhance maintenance operations over time.
This newsletter is based on an article by BY DOC PALMER, PE, MBA, CMRP, Plant Services (2022). For more insights and advice on maintenance planning and scheduling, visit IAMTech and explore our Knowledge Section.